Last
modified: 2004/05/27
OWL
DESIGN |
|
The
essential characteristics of OWL are, first, to integrate proven
technologies into a novel system concept and, second, to rely
extensively on serial, industrialized fabrication of identical
building blocks. As a result, technology development is limited
to few, well defined areas, and risks, costs and leadtime can
be kept within manageable limits. |
|
SETTING THE REQUIREMENTS
|
|
Design characteristics
|
Pupil size (diameter) |
100
|
m |
Collecting area |
> 6000
|
m2 |
Multi-conjugate Adaptive
Optics |
Diffraction-limited resolution
over field of view : |
__Visible
(0.5 mm) |
> 30
|
arc sec. |
__Infrared
(2 mm) |
> 2
|
arc min. |
Strehl ratio (at 0.5 mm) |
__Requirement |
20
|
% |
__Goal |
30
|
% |
Seeing-limited field of
view |
10
|
arc min. |
Wavelength range |
0.32-12
|
mm |
Elevation range |
__Operational |
30-89
|
degrees |
__Technical
|
0-90
|
degrees |
Maximum cost
(capital investment) |
1000
|
M€ |
|
|
OWL's objective is to provide both resolution and sensitivity
in a reliable and cost-effective manner. Individual science
objectives generally imply specific requirements, from which
system ones are derived. Because of the diversity of applications
and the limitations of technology, conflicting requirements
must be addressed by suitable trade-offs. As all scientific
objectives benefit from an increased aperture size, and because
the telescope size and cost are closely related, constraints
which would imply overcosts must be wighted against a decrease
of telescope diameter. This also applies to telescope engineering.
Performance cannot be measured in technical terms only; it
must encompass cost, leadtime, and risks.
OWL incorporates key fabrication technologies and system
solutions that are the trademarks of the current generation
of large, 8- to 10-m telescopes: active optics (NTT, VLT,
Subaru, Gemini); optical segmentation (Keck, Hobby-Eberly,
GTC, SALT), low-cost optics and structures (Hobby-Eberly,
SALT). The only feature which truly extrapolates from state-of-the-art
technology is adaptive optics.
The overall performance of a telescope depends not only on
the quality of its design and construction. Technical and
scientific operations must be taken into account right from
the initial design phases, with a view to maximizing uptime
and providing transparent operation. The user is ultimately
interested in science, not technology.
|
|
FRACTAL
DESIGN AND EARLY OPERATION |
|
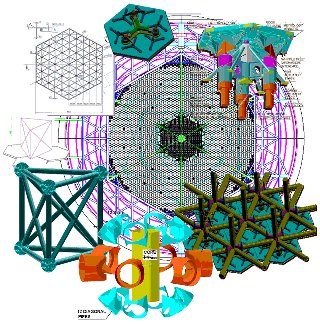 |
For reasons of cost and ease
of integration and maintenance, OWL design relies extensively
on serially produced components and modules
|
OWL's dimensions allow to rely extensively on
modular design, integration and maintenance, with large numbers
of identical parts, components and modules. As a result, construction
and operation costs are very low for a system of this size
and capability, and mutliple supply and integration lines
allow a fast construction schedule. Virtually all telescope
parts can be shipped to the site in standard 40ft containers.
All major dimensions are integer multiple of
the segments size, thereby simplifying interfaces and allowing
a distributed transfer of loads from the optics through substructures,
to the main structure and eventually to the foundations.
A byproduct of segmentation is that once the
enclosure, the telescope structure, kinematics, and control
systems are functional, the telescope can become operational
even though its primary mirror is not yet entirely filled.
Existing segmented telescopes have indeed been turned to the
sky before full completion, albeit for engineering runs only.
Those have, however, no more than 36 segments in total -compared
to 3048 for OWL. Optical fabrication is therefore no longer
on the critical path and engineering work will be essentially
completed at an early stage. The telescope will progressively
enter into science operation when its aperture will have reached
60m. At that point, OWL will be equipped with its first stage,
first generation adaptive optics for the compensation of atmospheric
turbulence, and thus be able to deliver unmatched scientific
results already. According to conservative estimates, this
could occur around 2017, with the telescope being completed
by 2021. A faster schedule would be possible, subject to early
funding.
|
|
OPTICAL
CONFIGURATION |
|
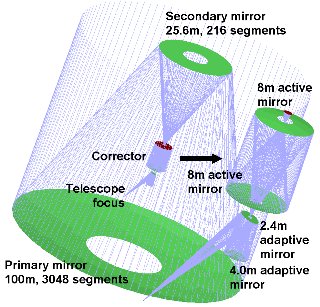 |
Layout of the OWL
optical design, with detailed view of the corrector (to
the right). Owl primary mirror would be made of 3048 segments |
|
The baseline design is comparable to that of the Hobbby-Eberly
telescope, the main difference being a secondary, segmented
flat folding mirror allowing a shorter structure. The 100-m
primary mirror will be made of 3048 heaxagonal, all-identical
segments, each 1.6-m in size. The 25.6-m secondary mirror
will be made of 216 flat segments, also 1.6-m large. The segments
will be made of low expansion glass-ceramics or silicon carbide.
Spherical and field aberrations are compensated by means
of a 4-elements corrector, conveniently located mid-way in
the telescope structure. The corrector includes two flexible
eight-meter class active mirrors (similar to the VLT primary
mirror), a 4.2-m focusing and a 2.35 flat, fast steering adaptive
mirror for first stage adaptive correction. The 4.2-m mirror
will eventually be replaced by an adaptive one, thereby permitting
the compensation of atmospheric turbulence over larger fields.
A crucial property of the design is that, contrarily to classical
designs, tight tolerances for alignment do not apply to the
(flat) secondary mirror, where the structural flexures will
need to be in the centimeter range -a figure deemed excellent
for a steel structure of OWL size. Instead, tight tolerances
apply to the alignment of surfaces inside the corrector, a
subsystem of large but still much more manageable size and
mass.
|
|
STRUCTURE
AND KINEMATICS |
|
 |
Design optimization is already
quite advanced, with much higher stiffness and lower mass
than initially thought. |
|
The telescope will have an alt-azimuthal steel structure, with
a moving mass of 14,200 tons. However impressive this figure
may seem, it should be noted that a conventional telescope design
extrapolated to OWL size would lead to about a million tons.
Detailed stress and fatigue analysis have shown that the OWL
design already meets the applicable safety requirements. Composite
materials will be used for tensioning cables and perhaps at
specific locations of the structure - provided that doing so
improves performance and safety at reasonable costs. The moving
mass could be reduced to about 8,500 tons if the segments were
made of silicon carbide.
The telescope will be mounted on friction drives (bogies)
"rolling" on steel tracks. A large (~300) number
of bogies will be used to distribute loads; each bogie will
be fitted with a standard motor. The drives will be hydraulically
connected to allow periodic (e.g. seasonal) re-adjustments.
|
|
A
CONTROLLED OPTO-MECHANICAL SYSTEM |
|
|
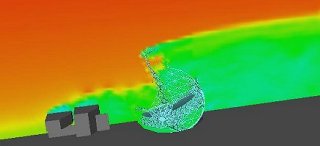 |
. |
Open air operation is ideal
for low thermal turbulence but requires active compensation
of the effect of dynamic wind pressure. |
|
|
|
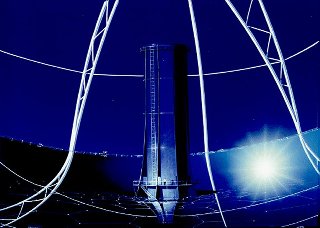 |
|
Keeping OWL 3264 segments aligned
to a few millionths of a millimeter is a daunting but
not impossible task (artist view, courtesy Ciel et Espace)
|
|
|
Modern telescopes are controlled opto-mechanical systems
whose optical characteristics are optimized in real time by
updating dedicated active subsystems, on the basis of error
signals measured by suitable metrology. Active optics, pioneered
by ESO in the 1980s with its 3.5m New Technology Telescope,
then with the 8-m VLT, is now a classical example of such
controlled system.
The conceptually simplest control system is that ensuring
that the telescope tracks i.e. that the effect of earth rotation
is properly compensated by the kinematics of the telescope.
With increasing size and tighter requirements, other control
systems must be implemented as the telescope can no longer
retain its properties passively. Permanent re-alignment and
focusing, fast correction of minute tracking errors, compensation
of residual fabrication errors and slowly varying flexures
of optical surfaces were implemented in the active optics
of the VLT, with great success. In a segmented telescope,
individual segments must, in addition, be actively supported
and kept aligned within extreme tolerances. The Keck telescope
was the first segmented one to enter into operation (1994);
the technique is proven, relies on fast evolving electro-mechanical
technologies, and is highly scalable.
The most challenging system is adaptive optics, which compensates
light wave distrubances generated by atmospheric turbulence.
To this end, a metrology system (wavefront sensor) located
at the focus of the telescope measures these disturbances,
and commands the shape of a moderately sized, thin deformable
mirror supported by thousands of fast actuators. The correction
must be repeated every few milliseconds, as turbulence changes
quickly. Bar unexpected technology development, OWL's first
generation of adaptive systems will work in the infrared,
where the correction requires a lower number of degrees of
freedom (actuators). At shorter wavelength, it will provide
partial correction only -except, perhaps, under conditions
of very low turbulence. A second, smaller but more complex
stage will be subsequently implemented for enhanced correction.
|
|
INSTRUMENTATION |
|
Developing the Instrument
suite that will address the major science drivers for such a
giant facility is bound to be extremely challenging. As an initial
complement, we are envisioning an Adaptive-Optics corrected
spectral analyzer with multiple "picker arms" to study
many small regions at once in the whole field, from individual
stars in nearby galaxies to the most distant galaxies and hypernovae,
and a high-contrast diffraction-limited spectro-imager to extract
and characterize planets around other Suns. Much like CERN for
high-energy physics, specialized instruments will in addition
be built by ad-hoc Consortia made of many Research Institutes
to specifically attack the new hot topics that will inevitably
come up in the years to come, out of the present generation
of ground-based and space-based Observatories spanning the full
electromagnetic spectrum. |
ESO Telescope Systems
Division
Karl-Schwarzschild-Strasse 2, D-85748 Garching, Germany
|
|